Machine Vision Systems
Unlock the full potential of your operations with our advanced industrial vision systems
Tailored Machine Visionfor Your Process Needs
At Adbro Controls, we understand that every business has unique needs and requirements when it comes to integrating machine vision solutions. That’s why we specialize in creating bespoke vision systems that are tailored to meet the specific needs of each customer. Our team of engineers and technicians work closely with our customers to understand their requirements and objectives, and to develop a customized solution that meets their needs.
We start by analysing the customer’s production process, identifying any areas where machine vision technology could be beneficial. We then design and build a system that incorporates the latest hardware and software technologies. Throughout the process, we work closely with the customer to ensure that the system meets their requirements and is optimized for their specific production environment. Our goal is to create vision system solutions that fully integrate with the customer’s production line, delivering reliable and consistent results.
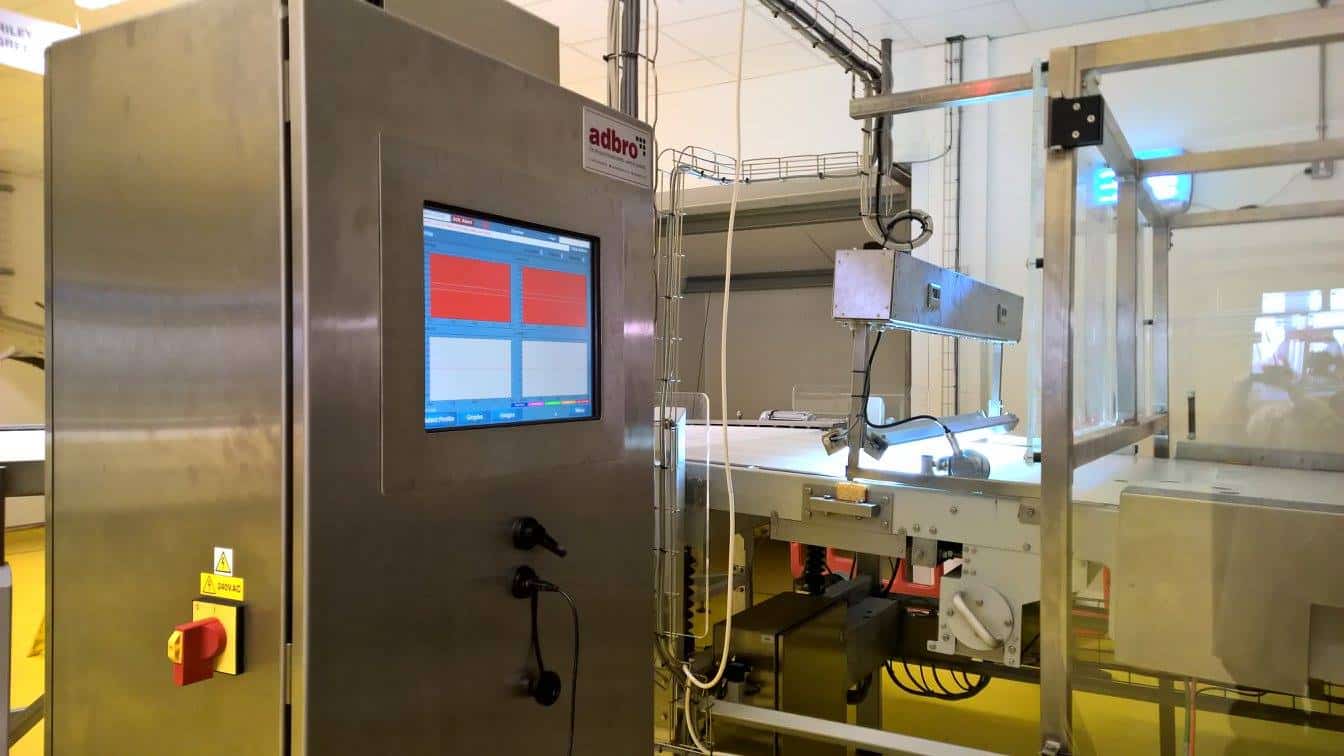
What Can Our Vision Systems Do for You?
- Automate inspection processes to improve efficiency and reduce the risk of human error
- Provide faster and more accurate detection of defects and abnormalities in products
- Improve quality control and ensure that products meet the highest standards of quality and consistency
- Minimize waste, rework, and scrap to reduce costs and improve the bottom line
- Easily scale to accommodate growing production needs and expanding operations
- Provide a competitive advantage by offering higher quality products, faster turnaround times, and lower costs
- Enable real-time monitoring and analysis of production processes to identify potential issues and improve overall performance
- Help businesses comply with industry regulations and standards by providing reliable and consistent inspection results
- Defect detection
- Gauging and precise measurement
- Completeness checks
- Surface inspection
- Code reading
- OCR
- Traceability and image archiving
- Robot guidance and position tracking
Some of the Types of Vision Inspection Systems We Provide
Deep Learning
Our deep learning (AI) technology leverages machine learning algorithms and training datasets to enable systems to learn and improve over time, delivering accurate and reliable results.
Various factors can affect the performance of a vision system, and one crucial consideration is the lighting conditions of the subject. This includes ambient lighting variances, product reflectance, and machine positioning. While designing a custom lighting setup can often overcome such issues, it may not always be the most practical or effective solution.
In situations like these, we employ deep learning techniques to train neural networks capable of identifying patterns where traditional methods fall short. The technology is tuned to analyse both “good” and “bad” images from your specific process. Our system then employs these classifiers as a guide when performing quality inspections and checks. The AI is trained robustly to make accurate decisions even in changing conditions.
In addition to its classification capabilities, deep learning excels at pattern matching, OCR (Optical Character Recognition), and image segmentation.
By analysing complex data, detecting patterns, and providing predictions, our deep learning solutions empower you to make informed decisions. Incorporating artificial intelligence into your vision system allows you to achieve a higher level of automation and efficiency while improving the accuracy and reliability of your processes.
3D Scanning
Our 3D scanning technology is designed to create detailed and highly accurate models of objects, surfaces, and environments. We employ various techniques such as sheet of light / laser triangulation, stereo vision, and time of flight depending on which is the best fit for the task at hand.
With our high-speed 3D vision systems, we can capture data in real-time, enabling businesses to achieve 100% inspection in high-speed production environments. By facilitating rapid data acquisition, processing, and analysis, our solutions ensure that critical information is available when needed most.
Whether you require precise measurements, defect detection, or part location, our 3D vision systems are tailored to address your unique requirements. By harnessing the power of 3D vision, businesses can achieve unparalleled accuracy, streamline processes, and make informed decisions to drive their operations forward.
Quality Inspection
When products fail to adhere to predefined standards, the consequent decrease in quality can lead to significant problems down the line. Issues might surface at later stages of production, causing costly downtime, or, even more concerning, they could manifest as customer complaints. More gravely, substandard products may pose safety hazards in certain scenarios. These potential risks reinforce the critical importance of maintaining rigorous standards enforced by quality inspection systems.
Our automated inspection systems helps ensure product quality and consistency, reducing the risk of defects and recalls. We use advanced detection algorithms to inspect products for defects and anomalies, with methods such as reject conveyors to remove non-conforming products from the production line.
Quality checks can include defects such as out of tolerance dimensions, colour variation, or unwanted marks and scratches can be detected. Furthermore, once defects have been identified, they can be analysed. This allows for a deeper understanding of the quantity, severity, and origin of the defects, providing invaluable insight for future improvements.
Measurement
Unlock precise and dependable measurements with our cutting-edge measurement systems. By utilizing high-resolution cameras, lasers, and advanced sensors, we capture data and provide accurate results. Seamlessly integrating into your operations, our systems enable you to optimize processes and elevate quality control to new heights.
Not only do our systems provide accurate measurements but they also offer trending and comparison capabilities. This allows operators to identify deviations from target specifications and make adjustments before processes veer too far off track. By catching and addressing deviations early, you can avoid product scrappage, minimize downtime, and optimize productivity.
Location Tracking
This vision technology is commonly integrated into pick and place systems, but it also finds applications in product sorting and alignment for processing purposes.
By detecting incorrect positioning, process equipment can make necessary adjustments or remove the product. This capability reduces the likelihood of machine jamming, protects essential equipment from excessive wear, and minimizes downtime.
Furthermore, our location tracking feature enables the prediction of future motion changes. Through intelligent programming, process equipment can proactively react to prevent issues before they arise, ensuring smooth operations and avoiding disruptions.
For more complex tracking tasks, our systems can capture 3D point clouds and match them to CAD models. This enables the identification of part versions, coordinates, and orientations. The obtained data can be utilized to determine pick points for robots, evaluate intricate geometries, and measure distances.
Remove Defects With Automated Reject Mechanisms
A vision system that can detect when an item is out of specification can be a vital component to your inspection process. However, once you’ve identified a substandard product, how can it be isolated and removed from the production line?
We offer a range of rejection systems to meet the needs of different industries and applications. Our systems are fully customizable and can be integrated seamlessly with your existing production line. If you are looking for a reliable and efficient way to manage defective products in your production line, contact us today to learn more about our reject systems and how we can help you improve your operations.
Why Choose Adbro Controls for Your Industrial Vision Systems?
We pride ourselves in being able to offer you bespoke vision systems that will meet your exact requirements. With so many years in the process industry, we have the knowledge and experience to consult with you as to what is best for your business.
- Expertise: Adbro Controls has extensive experience in developing and implementing machine vision solutions across a wide range of industries and applications. Our team of engineers and technicians are highly skilled and knowledgeable, and we are committed to delivering the highest level of expertise and service to our customers.
- Customization: We understand that every business has unique needs and requirements. That’s why we offer fully customizable inspection systems that can be tailored to meet the specific needs of each customer. From hardware and software to algorithms and interfaces, we can create a solution that works for you.
- Integration: Our automated vision systems are designed to integrate seamlessly with existing production lines and equipment, minimizing disruption and downtime. We work closely with our customers to ensure a smooth and efficient integration process and provide training and support to ensure that the system is operating at peak performance.
- Quality Assurance: At Adbro Controls, we are committed to delivering the highest level of quality and reliability in our machine vision solutions. We rigorously test our systems to ensure that they meet or exceed your standards.
- Support: We understand that machine vision technology can be complex, and that our customers may need support and assistance from time to time. That’s why we offer ongoing support and maintenance services to ensure that our customers’ systems are always operating at their best.
After contacting us with your requirement, a dedicated vision engineer will get in touch to discuss your needs in further detail. To enable us to advise the best solutions for you, a site visit can be scheduled where we can observe your process in situ.
In order to assist with the development side of the project, where possible we like to obtain product samples to help aid tests carried out in house. These tests will include the use of a range of equipment including cameras, lenses and lighting.
Results obtained by these test studies will enable us to determine the best solution for your needs and allow us to advise the associated costs.